Single-Axis Flexure Translation Stages: 1.5 mm Travel
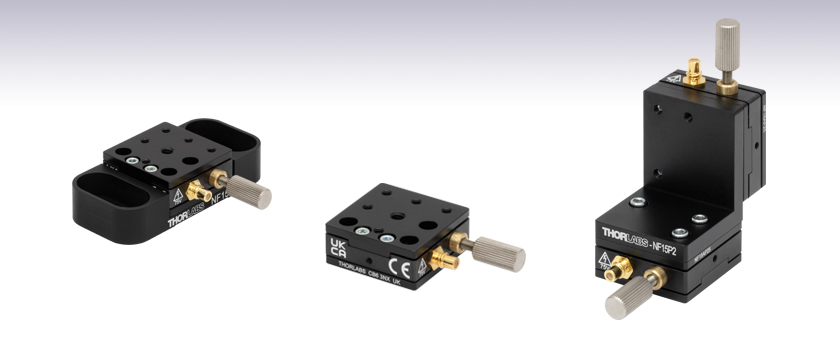
- Flexure Design - No Friction or Sticking
- Thumbscrew Adjuster and 25 µm Piezo Actuator
- Mounting Plate and Angle Bracket Available
NF15P1 Adapter
with NF15AP25
Stage
NF15AP25
NF15P2 Adapter with Two NF15AP25 Stages
Save 10% with
Stage and Controller Bundle
KPZNF15
NF15AP25 with KPZ101 Controller

Please Wait
Key Specificationsa | |
---|---|
Item # | NF15AP25(/M) |
Manual Travel | 1.5 mm (0.06") |
Adjuster Resolution | 0.25 mm/Revolution |
Load Capacity | Horizontal: 0.5 kg (1.1 lbs) Vertical: 0.25 kg (0.55 lbs) |
Cross Talk | 1.0 µm (Max) |
Piezo Travel | 25 µm |
Piezo Resolution (Theoretical) |
0.76 nm |
Piezo Voltage | 0 - 75 V |
Single-Axis Flexure Stage Selection Guide |
---|
1.5 mm Travel |
5 mm Travel |
Features
- Manual Translation Range: 1.5 mm
- Piezoelectric Translation Range: 25 µm
- Compact Size: 30.0 mm x 30.0 mm x 12.5 mm
- XYZ Configurable with Optional Base Plate and Angle Bracket
- Compatible Piezo Controllers: KPC101, BPC301, BPC303, MDT694B, MPZ601
Thorlabs' NanoFlex™ flexure stages are compact stages that offer translation without friction or sticking. The flexure mechanism used in these translation stages is a frictionless mechanism that has improved positioning and resolution when compared to similar stages made using bearings. The translation of the stage is accomplished by the elastic deformation (flexing) of a linkage attached to the mounting platform. The translation stage has a manual translation range of 1.5 mm with an independent piezoelectric translation range of 25 μm (see the Selection Guide tab for stages with 5 mm manual translation). Piezo connection is made by a standard SMC terminal. See the Selection Guide tab for our 1.5 mm manual translation stage.
The NanoFlex™ flexure stages are rated for a maximum load of 0.5 kg (1.1 lbs), which makes them an ideal choice for many laboratory and OEM applications. The modular design allows for multiple stages to be stacked in multi-axis configurations. An XYZ configuration can be constructed using three NF15AP25(/M) stages and an NF15P2(/M) angle bracket.
Item # | NF15AP25(/M) |
---|---|
Manual Travel Range | 1.5 mm (0.06") |
Thumbscrew Resolution | 0.25 mm per Revolution |
Load Capacity | Horizontal: 0.5 kg (1.1 lbs) Vertical: 0.25 kg (0.55 lbs) |
Maximum Cross Talk | 1.0 µm |
Piezo Travel | 25 µm |
Piezo Resolution (Theoretical) |
0.76 nm |
Piezo Voltage | 0 - 75 V |
Piezo Capacitance | 5 µF ± 30% (at 1 V, 1 kHz) |
Piezo Connector | SMC |
Piezo Cable Length | 3 m (9.8 ft) |
Compatible Piezo Controllers | KPC101, BPC301, BPC303, MDT694B, MPZ601 |
Piezo Connection
SMC Male
0 - 75 V
These specifications are for the stage used in a single-axis configuration. When translation stages are stacked to make multi-axis configurations the resolution of the positioning system is deteriorated by cosine and Abbe errors (crosstalk). The positioning error cause by the stacked stages not being orthogonal to each other is referred to as the cosine error while the Abbe error is due to the non-zero height of the stacked stage. This height leads to an amplification of any angular roll, pitch, or yaw errors in the base stage. These errors can be avoided by using a multi-axis translation stage where the degrees of freedom are controlled by parallel linkages. A variety of 3, 4, 5, and 6 axis stages can be purchased from Thorlabs in a wide variety of manual and automated configurations. For a 3-axis solution, consider our 3-axis flexure stages.
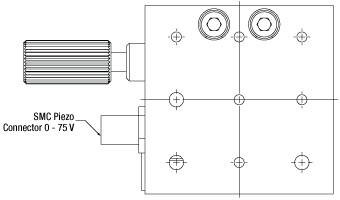
Piezo Connection
SMC Male
0 - 75 V
Posted Comments: | |
Andrea Sardella
 (posted 2024-03-02 16:04:19.423) Could you provide me a drawing with the travel direction for the piezo? I'm not sure I'm using in the correct way
Thanks spolineni
 (posted 2024-03-07 11:22:39.0) Thank you for your query. The travel direction is parallel with the advancement direction of the thumb screw adjuster. Nonetheless, I will contact you to provide a drawing for a more detailed understanding. Shay Keren-Zur
 (posted 2023-06-13 20:57:09.98) Hi,
I recently purchased the KPZNF15 stage bundle.
I realize that the control parameter is voltage, but I cannot find any reference regarding to the relation between the voltage value and the translation of the stage.
I'd be happy if you could support me on this matter.
Thanks,
Shay do'neill
 (posted 2023-06-15 07:59:49.0) Response from Daniel at Thorlabs. As there is no feedback for this stage it is not possible to equate a voltage to a position due to non linearity and more importantly hysteresis. It is possible to estimate the position as a linear relationship with the total travel range but to accurately know the position you will need to use some external way of measuring the position or choose a closed loop piezo stage Ben Carey
 (posted 2023-03-30 07:58:46.413) Hi I'm interested in using an NFP15AP25 to move a mirror. I already own an MDT694B piezo controller. I see the KPZ101 is the recommended driver for the stage. Is there any advantage to using the KPZ101 or will I be fine with the MDT694B? do'neill
 (posted 2023-03-31 11:07:11.0) Response from Daniel at Thorlabs. The compatible controllers for the NF15AP25 are the KPZ101, BPC301, BPC303, MDT694B, and MPZ601. The is no issue in using the MDT694B to control this stage. I will reach out to you to discuss your application. Xu yan
 (posted 2021-10-21 06:00:10.767) Hi, I recently bought an NF15AP25/M piezo stage with an NF15P1 adapter and a KPZ101 K-cube controller.
I fixed a mirror on the piezoelectric stage as an arm of the interferometer, but the mirror is very easy to shake and cause the interference fringe to shake. Is there any way to solve it?
In addition, I use KPZ101 for every 0.01V increase in voltage and the actual displacement is about 1.5nm instead of 0.76nm. What is the reason? YLohia
 (posted 2021-12-23 10:44:41.0) Hello, thank you for contacting Thorlabs. We are sorry to hear that you're having issues with this device. We have reached out to you directly to troubleshoot further. user
 (posted 2021-08-05 04:51:47.107) Hi, I recently bought an NF15AP25/M piezo stage with an NF15P1 adapter and a KPZ101 K-cube controller.
When I go from 0 to 75V using the K-cube controller, the piezo stage moves by approximately 15 µm instead of the 25 µm expected. Do you know where the problem may come from? DJayasuriya
 (posted 2021-08-05 09:30:16.0) Thank you for your inquiry. We will get in touch with you directly to resolve your issue. Matthias Steiner
 (posted 2020-08-05 07:18:21.17) Hi,
can the thumbscrew adjuster be replaced with a lock-able adjuster? cwright
 (posted 2020-08-10 10:12:03.0) Response from Charles at Thorlabs: Hello Matthias and thank you for contacting us. Unfortunately this is not something we can offer as a special request at this time but I will reach out to you to discuss how you may be able to add similar functionality. loo
 (posted 2016-03-09 17:13:11.81) Nothing seem attached from beneath the top plate of the flexure stage, beside the two screws to the square frame. So, is it possible to unscrew the top plate of the stage to have it machined, and then put it back together without damage? Or even unscrew it and replace it completely with a custom top plate of ours? besembeson
 (posted 2016-03-10 03:22:28.0) Response from Bweh at Thorlabs USA: No that is not possible. The top plate is also connected to the flexure mechanism inside. Removing that top plate could also cause misalignment so you are better off having a custom adapter plate to use on the top plate. gesuele
 (posted 2014-01-09 05:15:33.373) I am wondering if the NF15AP25 can be used as a raster scanning stage (two of them for XY scanning). What would be the maximum scanning rate? msoulby
 (posted 2014-01-09 05:39:13.0) Response from Mike at Thorlabs: Yes, using two of the NF15AP25 stages in an XY configuration can be programed to perform a raster scan. To do this you would need to use a programming environment such as Labview or Matlab using the ActiveX methods provided with our APT software. I have contacted you directly with an example of a 2D piezo raster scan LabView .VI and a guide on how to use our APT software in Labview.
Regarding the maximum scan rate this depends on the capacitance of the piezo element and the maximum output current of the piezo driver. Using the TPZ001 piezo controller, which has an output of 7.5mA a full scan from 0-75V (which represents zero to maximum piezo displacement of 0-25um), will give a maximum bandwidth of about 6Hz, for a sinusoidal input. Using the BPC301 which has an output drive current of 0.5A a maximum sinusoidal bandwidth for this piezo stage will be about 420Hz, full details can be found on the ‘Piezo Bandwidth’ tab on the TPZ001 product page. cwilson
 (posted 2013-08-18 07:32:08.187) Leaving Test Feedback after replication reset bdada
 (posted 2011-06-06 12:49:00.0) Response from Buki at Thorlabs:
Thank you for using our Feedback Tool. Unfortunately there is no direct solution for attaching the MS3/M to the NF15AP25/M. You can try other configurations like using the NF15P2 angle bracket to combine two NF15AP25 as shown on the webpage below:
http://www.thorlabs.com/NewGroupPage9.cfm?ObjectGroup_ID=787&pn=NF15P2#787
Please contact us at TechSupport@thorlabs.com if you want to discuss this matter further. stuchris
 (posted 2011-06-03 12:48:37.0) Hi, is there any way I can attach the NF15AP25/M to the MS3/M? Thanks. user
 (posted 2010-06-01 18:43:51.0) Response from Javier at Thorlabs to mabashin: The capacitance of the piezo used in the NF15AP25 is 5 uF +/- 30% (@1V, 1kHz) mabashin
 (posted 2010-06-01 17:37:50.0) What is the capacitance of the piezo on the NF15AP25? |
Manual Linear Translation Stages
Thorlabs' manual translation stages are offered in a range of maximum travel distances, from less than 1/4" (6 mm) to 2" (50 mm) and longer for our long travel, large area platforms. Many of these stages can be ordered in multi-axis configurations, providing XY or XYZ translation. For fiber coupling applications, please see our Multi-Axis Stages, which offer finer adjustment than our standard manual translation stages. In addition to linear translation stages, we offer rotation stages, pitch and yaw platforms, and goniometers. We also offer motorized translation stages that are powered by DC Servo motors, stepper motors, or direct drive technology.
Crossed-Roller Bearing Stages
These linear translation stages feature crossed-roller bearing travel mechanisms for precision motion, high load capacity, and low angular deviation. The LNR Series stages feature all-steel body construction, while the LX, XRN, and XR Series stage bodies are constructed of cast tool and jig aluminum. We also offer several vertical crossed-roller bearing stages (see Table 140E).
Table 140A Crossed-Roller Bearing Stages | ||||||
---|---|---|---|---|---|---|
Product Family | LNR Series 25 mm Stages |
LX Series 25 mm Stages |
XRN Series 25 mm Stages |
XR Series 25 mm Stages |
XR Series 50 mm Stages |
LNR Series 50.8 mm Stages |
Click Photo to Enlarge |
![]() |
![]() |
![]() |
![]() |
![]() |
![]() |
Travel | 25 mm (0.98") | 25 mm (0.98") | 25 mm (0.98") | 25 mm (0.98") | 50 mm (1.97") | 50.8 mm (2") |
Drive Type | Multiple | Micrometer | Micrometer | Micrometer | Micrometer | Multiple |
Platform Size | 2.34" x 2.36" (59.4 mm x 60.0 mm) |
2.56" x 2.56" (65.0 mm x 65.0 mm) |
2.00" x 3.35" (50.7 mm x 85.0 mm) |
2.98" x 4.33" (75.7 mm x 110.0 mm) |
2.98" x 5.51" (75.7 mm x 140.0 mm) |
3.94" x 3.94" (100.0 mm x 100.0 mm) |
Possible Axis Configurations |
X, XZ, XY, XYZ | X, XY, XZ, YZ, XYZ | X, Y, Z, XY, XZ, YZ, XYZ | X, Y, Z, XY, XZ, YZ, XYZ | X, Y, Z, XY, XZ, YZ, XYZ | X, XY, XYZ |
Additional Details |
Ball Bearing Stages
These translation stages feature hardened steel linear bearings for precise motion and long life. They are available with a variety of actuators and in single-axis or preassembled multi-axis configurations.
Table 140B Ball Bearing Stages | |||||
---|---|---|---|---|---|
Product Family | MS Series 1/4" Stages | T12 Series 1/2" Stages | MT Series 1/2" Stages | PT Series 1" Stages | LT Series 2" Stages |
Click Photo to Enlarge | ![]() |
![]() |
![]() |
![]() |
![]() |
Travel | 1/4" (6.4 mm) | 1/2" (12.7 mm) | 1/2" (12.7 mm) | 1" (25.4 mm) | 2" (50 mm) |
Drive Type | Multiple | Thumbscrew | Multiple | Multiple | Differential Micrometer |
Platform Size | 1.17" x 1.17" (29.7 mm x 29.7 mm) |
0.76" x 0.81" (19.3 mm x 20.6 mm) |
2.40" x 2.41" (61.0 mm x 61.2 mm) |
3.00" x 4.00" (76.2 mm x 101.6 mm) |
3.75" x 3.75" (95.3 mm x 95.3 mm) |
Possible Axis Configurations | X, XY, XYZ | X, XY, XYZ | X, XY, XYZ | X, XY, XYZ | X, XY, XYZ |
Additional Details |
Dovetail Stages
These compact stages incorporate dovetails and a leadscrew for the translation mechanism. They are suitable in general purpose motion control applications.
Table 140C Dovetail Stages | |||
---|---|---|---|
Product Family | DT Series 1/2" Stages | DTS Series 1" Stages (Vacuum-Compatible Version Available) |
DTS Series 2" Stage |
Click Photo to Enlarge | ![]() |
![]() |
![]() |
Travel | 1/2" (12.7 mm) | 1" (25 mm) | 2" (50 mm) |
Drive Type | Thumbscrew | Thumbscrew | Thumbscrew |
Platform Size | 1.00" x 1.00" (25.4 mm x 25.4 mm) | 2.68" x 2.95" (68.0 mm 75.0 mm) | 2.68" x 3.74" (68.0 mm x 95.0 mm) |
Possible Axis Configurations | X, XY, XYZ | X, XY, XYZa | X, XY, XYZ |
Additional Details |
Flexure Stages
Thorlabs' Nanoflex™ translation stages feature frictionless flexure mechanisms for improved positioning and resolution when compared to similar stages made using bearings. The translation of the stage is accomplished by the elastic deformation (flexing) of a linkage attached to the mounting platform. Most models also include piezo actuators for small position adjustments.
Table 140D Flexure Stages | ||||
---|---|---|---|---|
Product Family | Nanoflex™ 1.5 mm Stage | Nanoflex™ 5 mm Stages | ||
Click Photo to Enlarge | ![]() |
![]() |
![]() |
![]() |
Travel | 1.5 mm (0.06") + 25 µm Piezo | 5 mm (0.20") | 5 mm (0.20") + 20 µm Piezo | |
Drive Type | Thumbscrew and Piezo Actuator | Differential Micrometer | Differential Micrometer and Open-Loop Piezo Actuator |
Differential Micrometer and Closed-Loop Piezo Actuator |
Platform Size | 1.18" x 1.18" (30.0 mm x 30.0 mm) | 2.95" x 2.95" (75.0 mm x 75.0 mm) | ||
Possible Axis Configurations | X, XY, XYZ | X, XY, XYZ | X, XY, XYZ | X, XY, XYZ |
Additional Details |
Vertical Stages
We offer vertical translation stages with crossed-roller bearings for precise motion as well as long travel vertical stages for heavy-duty applications.
Table 140E Vertical Stages | ||||||
---|---|---|---|---|---|---|
Product Family | XRN Series 9 mm Vertical Stage |
XR Series 14 mm Vertical Stage |
MVS Series 1/2" Vertical Stage |
MVS Series 1" Vertical Stage |
VAP Series 4" Vertical Stage |
VAP Series 10" Vertical Stage |
Click Photo to Enlarge | ![]() |
![]() |
![]() |
![]() |
![]() |
![]() |
Travel | 9.0 mm (0.35") | 14.0 mm (0.55") | 1/2" (13.0 mm) | 1" (25.0 mm) | 4" (101.6 mm) | 10" (254 mm) |
Drive Type | Worm-Gear Driven Lift Screw | Micrometer | Adjuster Knob and Coarse Manual Positioning | |||
Platform Size | 2.00" x 2.00" (50.7 mm x 50.7 mm) |
2.98" x 2.98" (75.7 mm x 75.7 mm) |
2.36" x 2.36" (60.0 mm x 60.0 mm) | 3.00" x 6.00" (76.2 mm 152.4 mm) | ||
Additional Details |
Motorized Linear Translation Stages
Thorlabs' motorized linear translation stages are offered in a range of maximum travel distances, from a stage with 20 µm of piezo translation to our 600 mm direct drive stage. Many of these stages can be assembled in multi-axis configurations, providing XY or XYZ translation. For fiber coupling applications, please see our multi-axis stages, which offer finer adjustment than our standard motorized translation stages. In addition to motorized linear translation stages, we offer motorized rotation stages and goniometers. We also offer manual translation stages.
Piezo Stages
These stages incorporate piezoelectric elements in a variety of drive mechanisms. ORIC® stages incorporate piezo inertia drives that use "stick-slip" friction properties to obtain extended travel ranges. Our Nanoflex™ translation stages use standard piezo chips along with manual actuators. Elliptec® stages use resonant piezo motors to push and pull the moving platform through resonant elliptical motion. Our LPS710E z-axis stage features a mechanically amplified piezo design and includes a matched controller.
Piezoelectric Stages | ||||
---|---|---|---|---|
Product Family | ORIC® PDXZ1 Closed-Loop 4.5 mm Vertical Stage |
ORIC® PD2 Open-Loop 5 mm Stage |
ORIC® PDX2 Closed-Loop 5 mm Stage |
ORIC® PDX4 Closed-Loop 12 mm Stage |
Click Photo to Enlarge |
![]() |
![]() |
![]() |
![]() |
Travel | 4.5 mm | 5 mm | 12 mm | |
Speed | 1 mm/s (Typ.)a | 10 mm/s (Typ. Max)b | 8 mm/s (Typ.)c | 15 mm/s (Typ.)a,c |
Drive Type | Piezoelectric Inertia Drive | |||
Possible Axis Configurations | Z | X, XY, XYZ | ||
Mounting Surface Size |
45.0 mm x 42.0 mm | 13.0 mm x 13.0 mm | 13.0 mm x 23.0 mm | |
Additional Details |
Piezoelectric Stages | |||||||
---|---|---|---|---|---|---|---|
Product Family | ORIC® PD1 Open-Loop 20 mm Stage |
ORIC® PD1D Open-Loop 20 mm Monolithic XY Stage |
ORIC® PDX1 Closed-Loop 20 mm Stage |
ORIC® PDX1A Closed-Loop 20 mm Stage Low-Profile |
ORIC® PD3 Open-Loop 50 mm Stage |
ORIC® PDX3 Closed-Loop 50 mm Stage |
|
Click Photo to Enlarge |
![]() |
![]() |
![]() |
![]() |
![]() |
![]() |
|
Travel | 20 mm | 50 mm | |||||
Speed | 3 mm/s (Typ. Max)a | 20 mm/s (Typ. Max)c | 10 mm/s (Typ.)b | 10 mm/sd | 10 mm/s (Typ. Max)b | ||
Drive Type | Piezoelectric Inertia Drive | ||||||
Possible Axis Configurations | X, XY, XYZ | XY, XYZ | X, XY, XYZ | X, XY, XYZ | X, XY, XYZ | X, XY, XYZ | |
Mounting Surface Size |
30 mm x 30 mm | 80 mm x 30 mm | |||||
Additional Details |
Piezoelectric Stages | |||||||
---|---|---|---|---|---|---|---|
Product Family | Nanoflex™ 20 µm Stage with 5 mm Actuator |
Nanoflex™ 25 µm Stage with 1.5 mm Actuator |
Compact Modular XRN25X 25 mm Stage |
Modular XR25X 25 mm Stage |
Elliptec® 28 mm Stage | Elliptec® 60 mm Stage | LPS710E 1.1 mm Vertical Stage |
Click Photo to Enlarge |
![]() |
![]() |
![]() |
![]() |
![]() |
![]() |
![]() |
Travel | 20 µm + 5 mm Manual | 25 µm + 1.5 mm Manual | 25 mm | 28 mm | 60.0 mm | 1.1 mm | |
Maximum Velocity | - | ≤3.6 mm/mina | 180 mm/s | 90 mm/s | - | ||
Drive Type | Piezo with Manual Actuator | Piezoelectric Inertia Drive | Resonant Piezoelectric Motor | Amplified Piezo | |||
Possible Axis Configurations | X, XY, XYZ | X, XY, YZ, XZ, XYZ | X | Z | |||
Mounting Surface Size | 75 mm x 75 mm | 30 mm x 30 mm | 85.0 mm x 50.7 mm | 110.0 mm x 75.7 mm | 15 mm x 15 mm | 21 mm x 21 mm | |
Additional Details |
Stepper Motor Stages
These translation stages feature removable or integrated stepper motors and long travel ranges up to 300 mm. Many of these stages either have integrated multi-axis capability (PLSXY) or can be assembled into multi-axis configurations (PLSX, LNR Series, NRT Series, and LTS Series stages). The MLJ150 stage also offers high load capacity vertical translation.
Stepper Motor Stages | |||||
---|---|---|---|---|---|
Product Family | PLSX with and without PLST(/M) Top Plate 1" Stage |
PLSXY with and without PLST(/M) Top Plate 1" Stage |
LNR Series 25 mm Stage |
LNR Series 50 mm Stage |
|
Click Photo to Enlarge |
![]() |
![]() |
![]() |
![]() |
|
Travel | 1" | 25 mm | 50 mm | ||
Maximum Velocity | 7.0 mm/s | 2.0 mm/s | 50 mm/s | ||
Possible Axis Configurations |
X, XY | X, XY, XYZ | X, XY, XYZ | ||
Mounting Surface Size |
3" x 3" | 60 mm x 60 mm | 100 mm x 100 mm | ||
Additional Details |
Stepper Motor Stages | ||||||
---|---|---|---|---|---|---|
Product Family | NRT Series 100 mm Stage |
NRT Series 150 mm Stage |
LTS Series 150 mm Stage |
LTS Series 300 mm Stage |
MLJ250 50 mm Vertical Stage |
|
Click Photo to Enlarge |
![]() |
![]() |
![]() |
![]() |
![]() |
|
Travel | 100 mm | 150 mm | 150 mm | 300 mm | 50 mm | |
Maximum Velocity | 30 mm/s | 50 mm/s | 3.0 mm/s | |||
Possible Axis Configurations |
X, XY, XYZ | X, XY, XYZ | Z | |||
Mounting Surface Size |
84 mm x 84 mm | 100 mm x 90 mm | 148 mm x 131 mm | |||
Additional Details |
DC Servo Motor Stages
Thorlabs offers linear translation stages with removable or integrated DC servo motors. These stages feature low profiles and many can be assembled in multi-axis configurations.
DC Servo Motor Stages | ||||
---|---|---|---|---|
Product Family | MT Series 12 mm Stages |
PT Series 25 mm Stages |
MTS Series 25 mm Stage |
MTS Series 50 mm Stage |
Click Photo to Enlarge |
![]() |
![]() |
![]() |
![]() |
Travel | 12 mm | 25 mm | 25 mm | 50 mm |
Maximum Velocity | 2.6 mm/s | 2.4 mm/s | ||
Possible Axis Configurations | X, XY, XYZ | X, XY, XYZ | ||
Mounting Surface Size |
61 mm x 61 mm | 101.6 mm x 76.2 mm | 43 mm x 43 mm | |
Additional Details |
DC Servo Motor Stages | ||||
---|---|---|---|---|
Product Family | M30 Series 30 mm Stage |
M30 Series 30 mm Monolithic XY Stage |
M150 Series 150 mm XY Stage |
KVS30 30 mm Vertical Stage |
Click Photo to Enlarge |
![]() |
![]() |
![]() |
![]() |
Travel | 30 mm | 150 mm | 30 mm | |
Maximum Velocity | 2.4 mm/s | X-Axis: 170 mm/s Y-Axis: 230 mm/s |
8.0 mm/s | |
Possible Axis Configurations | X, Z | XY, XZ | XY | Z |
Mounting Surface Size |
115 mm x 115 mm | 272.4 mm x 272.4 mm | 116.2 mm x 116.2 mm | |
Additional Details |
Direct Drive Stages
These low-profile stages feature integrated brushless DC servo motors for high speed translation with zero backlash. When no power is applied, the platforms of these stages have very little inertia and are virtually free running. Hence these stages may not be suitable for applications where the stage's platform needs to remain in a set position when the power is off. We do not recommend mounting these stages vertically.
Direct Drive Stages | |||||
---|---|---|---|---|---|
Product Family | DDS Series 50 mm Stage |
DDS Series 100 mm Stage |
DDS Series 220 mm Stage |
DDS Series 300 mm Stage |
DDS Series 600 mm Stage |
Click Photo to Enlarge |
![]() |
![]() |
![]() |
![]() |
![]() |
Travel | 50 mm | 100 mm | 220 mm | 300 mm | 600 mm |
Maximum Velocity | 500 mm/s | 300 mm/s | 400 mm/s | 400 mm/s | |
Possible Axis Configurations | X, XY | X, XY | X | X | |
Mounting Surface Size | 60 mm x 52 mm | 88 mm x 88 mm | 120 mm x 120 mm | ||
Additional Details |

The stages are supplied with a thumbscrew adjuster which provides manual adjustment and a 25 µm piezo actuator. The NF15AP25(/M) stages are ideal for a variety of laboratory and OEM applications. The NF15AP25(/M) translation stages are shipped with three M2 cap screws, an Allen key, and a 3 m long male SMC to male SMC cable.
See the Specs tab above for more detailed information including compatible controllers.

- Build XY, XZ, and XYZ Configured Stages
- Angle Bracket for Vertical Mounting
The NF15P1(/M) and NF15P2(/M) are adapter plates designed for the NF15(/M) Series of translation stages. The NF15P1(/M) is a special base plate designed to fit the NF15 Series translation stages with slots on the side that enable obstruction-free mounting onto an optical breadboard. This base is ideal for XY or XYZ multi-axis configurations where the standard counterbores in the middle of the stages are obstructed.
The NF15P2(/M) is an angle bracket that allows a NF15 Series stage to be mounted vertically. This is necessary in some XY and all XYZ configurations.